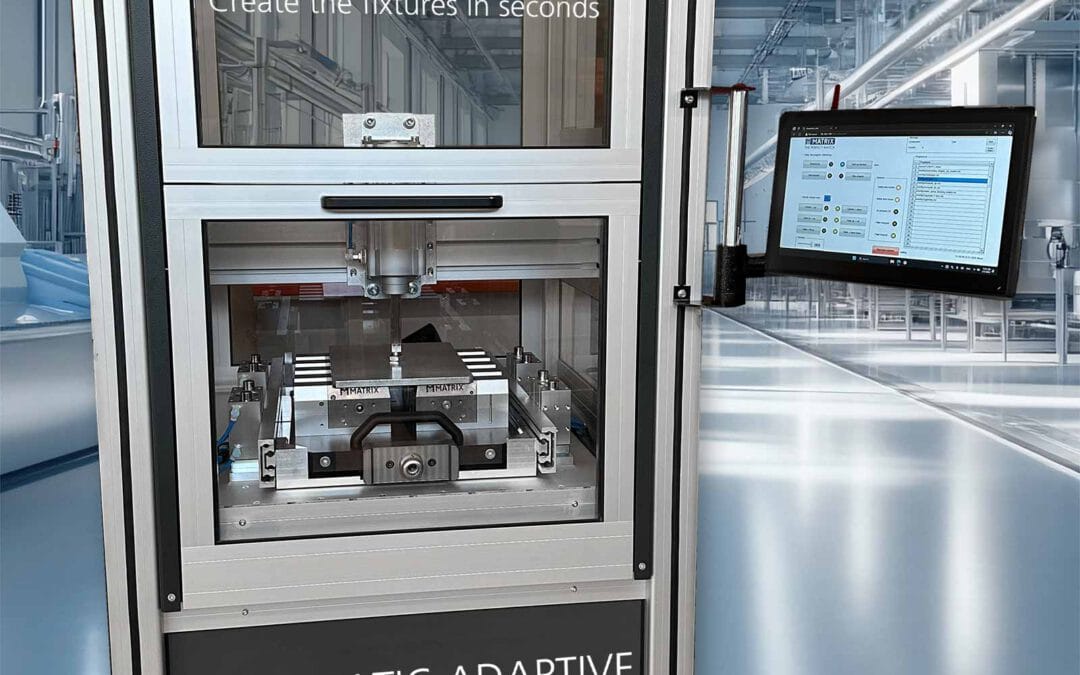
From Workholding Manufacturer to Machine Builder
From Workholding Manufacturer to Machine Builder
Step up to MATRIX®
In recent weeks, MATRIX successfully delivered its first machine featuring the innovative FLEXSTATION technology. The recipient of this state-of-the-art solution is a U.S.-based aerospace company.
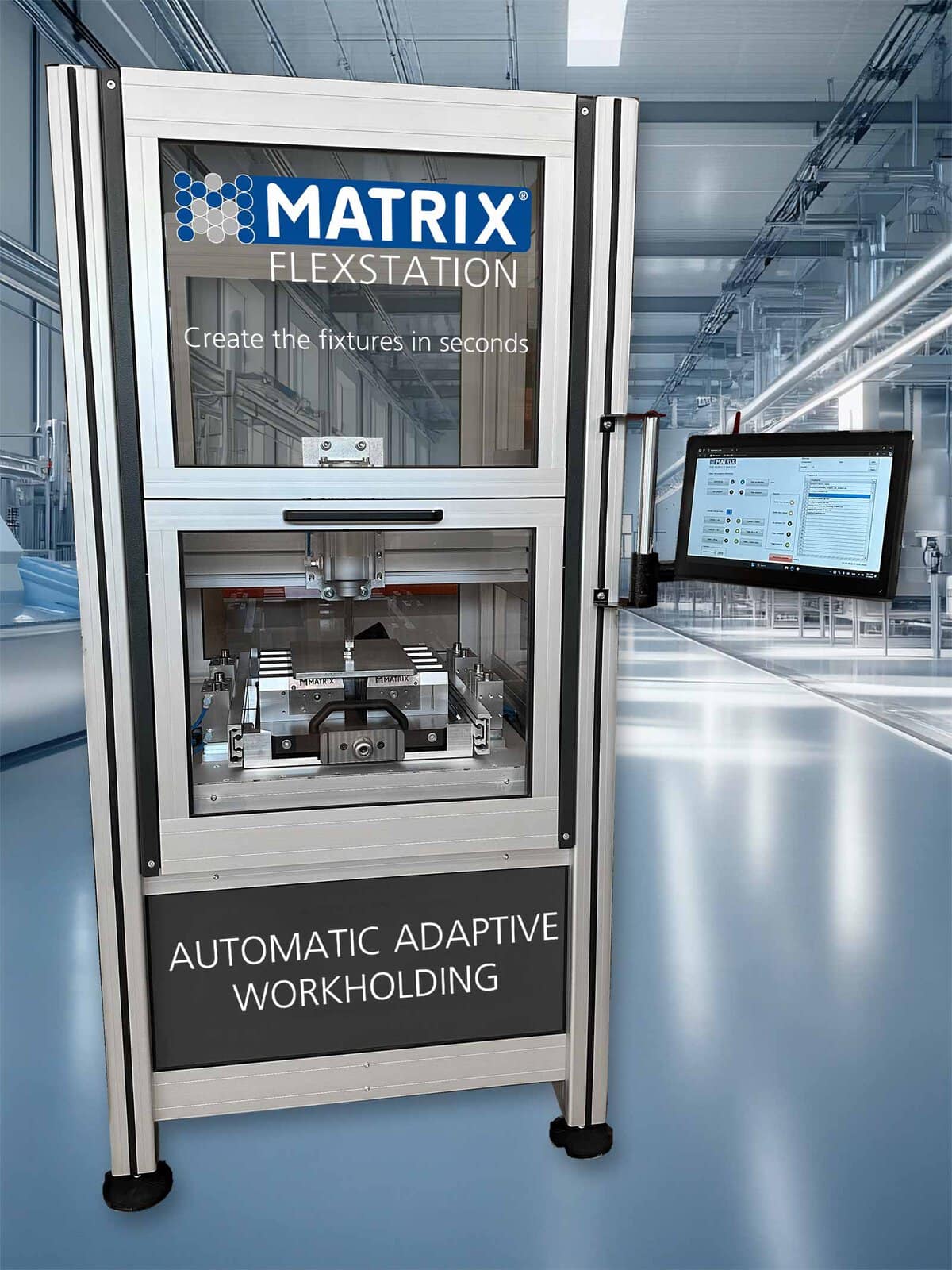
Innovation for Maximum Flexibility
With the ever-increasing complexity and variety of components to be manufactured, the demand for highly flexible production solutions is also growing. At the same time, the level of automation in modern manufacturing facilities continues to rise. To meet these evolving needs, MATRIX has consistently advanced the technology of adaptive clamping systems.
The next step from MATRIX transforms our conventional clamping systems into intelligent tools through innovative software integration. A single programmable MATRIX fixture can replace hundreds of specific fixtures—representing a paradigm shift that significantly reduces costs for end-users.
FLEXSTATION – A New Dimension in Fixtures
The MATRIX software enables individual definition and customization of fixture and workpiece carrier shapes. With just a push of a button, the configured shape is transferred to the FLEXSTATION, which sets up the MATRIX fixture precisely, consistently, and fully automatically. Regular software updates ensure that MATRIX customers always benefit from the latest technological advancements.
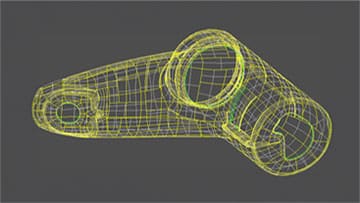
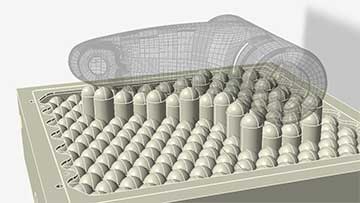
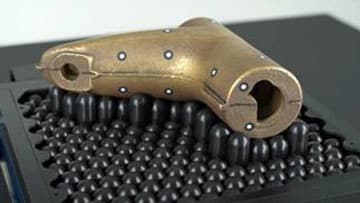
Your Partner for the Future of Manufacturing
With FLEXSTATION and intelligent clamping technology, MATRIX opens entirely new possibilities in production and measurement technology. Our team of experts is happy to provide individual consultations to find the optimal solution tailored to your needs.